Bonjour,
réponse à tes remarques
Le belge a écrit:Salutatous !
Cristop a écrit: ...puis une fois mastiquée à l'extérieur (syntofer 2 composants) j'ai imprégné intérieur et extérieur de résine époxy...
Heu... 'va falloir que tu m'expliques comment tu IMPREGNES du syntofer... surtout que tu dis utiliser plusieurs couches de résine de moins en moins diluée (quoique si tu y mets de l'acétone tu ne la dilues pas mais tu la dissous...), ce qui est la méthode pour imprégner à coeur un produit POREUX, ce que n'est pas le syntofer...
Tu a parfaitement raison j'ai manifestement écrit l'inverse de ce que j'ai fais toute mes excuses en plus il n'est pas très recommandé de passer une base polyester telle que les saint "O" ou solobibule à bi composants direct sur le bois, ce dernier va pomper l'un des composants, la présence d'eau dans le bois va freiner la réaction de polymérisation etc on risque donnc d'avoir une cocquille peu adhérante sur le bois. On peut s'en tirer en gavant le bois de styrène et faire ainsi déscendre la couche dans le bois mais c'est pas top pour la santé et on trouve plus sur et performant (le polyester est plutôt cassant même s'il est agréable à poncer)
Donc imprégnation à l'époxyde puis après application du polyester on peut (ce que j'ai fais ) repasser une couche non diluée d'époxydes.
Le belge a écrit: Cristop a écrit: ...résine époxy d'abord très diluée (1/10) à l'acool ménager + acétone en plusieurs couches de moins en moins diluées jusqu'à saturation du bois.
Ben c'est ce que le G4 permet de faire (saturer le bois) mais avec 2 produits (le G4 et son DILUANT) qui ne modifient pas les propriétés chimiques principales, au lieu de 4 produits dont un qui dégrade les propriétés chimiques principales... (en l'occurrence l'acétone, qui n'a jamais rien dilué, qui ne dilue rien, et qui ne diluera jamais rien, mais qui DISSOUT).
'Vois pas trop l'intérêt...
Anvant d'aller plus loin et pour raison d'éthyque et de transparance je signale que j'ai travaillé pour le chimiste historique fournisseur des monomères (TDI, HDI) employés dans toutes bases polyuréthane en l'ocurance du G4.
Donc l'usage du G4 (que je pourrais recommander massivement pour faire fructifier mon épargne salariale...) va effectivement permetre de saturer plus ou moins superficiellement le bois avec une résine polyuréthane. Le G4 est essentiellement basé sur un monomère TDI
(c'est un isocynate) il peut être fabriqué par exemple là, près de Grenoble (atelier HDI vu de l'atelier TDI)atelier vendu récemment à Perstop.
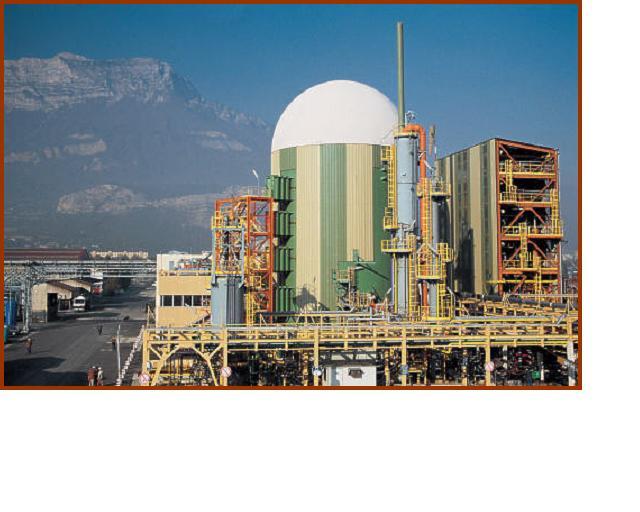
De ce fait la résine G4 sera plus flexible et moins résistante et par la même sensible à la lumière, ce qui n'aurait pas été le cas si le G4 etait sur la base HDI bien plus résistante mécaniquement et stable vis à vis des UV. C'est lui qui est utilisé pour peindre les voiture haut de gamme et les avions par exemple c'est le procédé concurant à la peinture époxyde pour situer le niveau de qualité de l'HDI par rapport au TDI.
Donc ce que je n'aime trop pas avec le G4 pour l'usage d'une coque c'est :
1/ la faible résistance mécanique (même si c'est déjà un gros plus) du polyuréthane employé
2/ Le risque de ne pas imprégner en profondeur le bois surtout si celui-ci est très humide, le TDI se polymérise grâce à la présence de l'eau et va constituer une sorte de barière au sein des fibres surtout si le bois est humide surtout s'il fait chaud, le G4 contient un solvant qui permet de diluer l'eau et de la "sortir" par afinité, en quelque sorte, mais le mélange est quand même un peu visqueu pour pénétrer facilement dans des bois chargés et "sérés". Pour parfaire cette action certains chimistes comme Voss vendent un solvant spécifique pour diluer le monomère et pénétrer plus surement en sortant la charge organique et acqueuse contenue dans le bois.
Je conseille vivement d'utiliser le solvant spécifique car il faut un solvant(certainement un mélange) particulièrement anhydre (sans eau) pour éviter la polymérisation lors du mélange, ce qui n'est pas le cas des solvant vendu dans le commerce qui contiennent de l'eau (certe pas beaucoup) et sont de ce fait pas recommandable avec le procédé G4 (d'autant que la qualité peut varier d'un lot à l'autre c'est pas du normapur pour analyse labo...).
Pourquoi l'époxy plus que le G4 ?
1/ la résistance mécanique, on a une méilleure résistance mécanique, la résine est encore un peu souple ce qui la rend pas cassante comme le polyester.
2/Le procédé de polymérisation robuste vis à vis du bois et vis à vis de la source en solvents "domestique" pour le diluer
J'ai fais l'expérience d'imprégner une baguette de balsa de 10 mm d'épaisseur la différence est flagrante entre G4 et époxyde si l'on imprègne qu'une face, le premier durci en surface les 2-3 premier mm mais s'écrase facilement sous la pression d'un doigt, pour l'autre il faut appuyer fortement pour marquer le bois et ne s'écrase pas vu que la résine est "allée" dans la masse complète .
Le choix des solvents il doit être compatible avec le procédé de polymérisation et le mileu que l'on souhaite imprégner. Je n'est pas compris sur le forum cette étiquette de dissoudre pour l'acétone, j'ai mon idée il y aurait une histoire de caoutchouc

mais l'analyse du phénomène n'est pas la bonne : le caoutchouc n'est pas une molécule unique ou un "mono" polymère c'est un sorte d'alliage, l'acétone va détruire cet alliage en séparant certains composés, comme si on cassait un mur, on a rien perdu c'est toujours de la pierre et du mortier mais la structure solide n'est plus là.
Si j'en crois la définition (non académique) industrielle chez les chimistes, dissoudre c'est faire passer (on pourra dire faire disparaître) en solution homogène liquide, une substance solide ou gazeuse. Donc n'importe quel solvant est capable de dissoudre quelque chose, mais pas toute les choses.
Les composés de la résine époxyde étant déjà liquides ils ne peuvent être dissous dans un solvant, et comme on parle de solvant on ne peut que diluer la résine par ajout de solvant si tel n'est pas le cas c'est le solvant n'st pas un solvant pour la résine, Ce qui nous ammène à dire ce que c'est qu'un solvant et une dilution.
Solvant, c'est un produit (ou un mélange) qui à la faculté de disperser des molécules sans les transformer chimiquement et qui par sa disparition permet de retrouver l'état chimique (très important car ne tient pas compte de l'organisation des molécules) des produits qui ont été dispersé.
Pour avoir l'atribut de solvant le dit produit, doit être majoritaire et ne pas réagir chimiquement (on tolère dans l'industrie sous cette appélation un faible tau de conversion chimique).
Par abus de language on qualifie de solvant les produits utilisés industriellement pour cet usage
l'acétone est qualifié de solvant, seul il est solvant de rien du tout (ci ce n'est de trace d'eau et des gaz dissous)
Les solvant sont classés en 4 familles dont une récente
tu a les Apolaires (non polaires)aprotiques , tel le toluène, benzène Xylène, cyclohexane..
Les polaires protiques : eau, alcools, acides...
Les polaires aprotiques dont l'acétone le THF (tétrahydrofurane) le DMSO etc...
Et les fameux liquides ioniques.
Dèrière ces noms barbares se cachent des propriétés physiques qui vont permettre de remplir certaines fonctions
miscibilité, dissolution volatilité tension superficielle etc...
La dilution est l'action qui consiste à réduire la concentration d'une molécule dans une autre
ajouter du solvant c'est forcément diluer c'est comme "monter en haut ou déscendre en bas" par abus de language on qualifie certains solvant de diluant car l'on souhaite par dilution faire tendre les propriétés apparente d'un mélange vers celle du solvant
idéalement il faudrait un solvant capable de pénétrer dans le bois (faible tension de surface, faible viscosité, pas trop volatil...) capable de dissoudre avec les composés chimique présent dans le bois (sucres, phénols, tanins goudrons, résines, gommes, graisses provenant de diverses contaminations...) ou de se mélanger aux substances liquides absorbées dans le bois(alcools, eau de 5 à 15%,...) et ainsi diluer tout celà et l'extraire pour saturer à son maximum le bois avec la résine en cours de polymérisationt(partiellement) du bois. Par dessus tout le solvant doit être économique, sans grand risque de manipulation, et présenter une toxycologie "acceptable". Et pour pousser le tout il faut être compatible avec le procédé de polymérisation et ne pas le dégrader chimiquement
Il n'existe pas un solvant sur l'étagère du supermarché qui répond à ce cahier des charges on va donc constituer
un mélange mais un mélange logique.
Ce mélange existe déjà industriellement depuis des lustres avant l'arrivée massive de solvants fluorés, c'est le mélange Toluène-alcool-Acétone ce ternaire ne laisse rien au hazard il est miscible et homogène il peut se mélanger à l'eau et donc la diluer , dissoudre éfficacement les graisses etc..
Le toluene seul ne serait pas interressant contrairement à ce que j'ai pu lire sur la revue historique, car il ne permettrait de sortir l'eau contenue dans le bois, pire il ne migrera pas vers les celulles saturée en eau, par contre, la présence de solvants polaires à ce produit, tel l'acétone et l'alcool va permetre de diluer l'eau et l'extraire en repoussant la démixion (une phase organique et une phase acqueuse).
Toutefois le toluene ne se trouve pas facilement et est sur ma liste noire des solvants (toxicité à divers niveaux et peut priver bibi d'une déscendance).
Le mélange se réduit alors à l'alcol acétone (2/3-1/3) (utilisé en labo biologie pour des tests analytique ) combinant un solvant aprotique et protique. pour faire simple l'ajout de l'acétone étand le spectre de solubilité de l'alcool (dissolution des graisses par exemple même si c'est pas ce qui se fait de mieux).
Ce mélange n'altère pas chimiquement la résine époxyde et le durcisseur.
Cette soupe permet donc d'extraire significativement les comoposés présents dans le bois par dissolution/dilution etd'apporter le mélange résine + durcisseur qui pourra polymériser au plus profond du bois surtout si l'on choisit une formule lente.
C'est une solution qui peut être un peu plus lourde et luxueuse que le G4 mais on étanche et durci à un niveau supérieur sans se ruiner (vu les prix du G4 chez certains détaillants) et sans se bousiller rapidement et à coup sur la santée.
La résine époxyde se conserve plus longtemps que le G4 après ouverture.
Pour ma part une coque dont je veux étancher et améliorer la résistance c'est résine époxyde, pour protéger de l'humidité des superstructures c'est plutôt G4 (enfin c'est surtout ce que j'ai sous la main).
Tout ceci pour dire que si on veut aller au bout du bout avec de petit moyens certains choix se font sur une certaine logique, c'est domage d'utiliser un produit et de ne pas exploiter complètement ses possibilité, après tu pourra me dire je vois pas une grande différance dans le résultat final sur une coque de 2-3 mm d'épaisseur et le pire c'est que tu aurra raison mais tu m'a demandé une explication vis à vis de mes choix je t'en donne une, bien que ce choix n'est pas de ma pure initiative car pratiqué industriellement depuis des lustres.
j'espère que j'ai pas trop écris de co***ries et que c'est assez compréhensible, il faut comprendre que lorsque l'on est dans l'industrie chimique, on a parfois l'impression que ce n'est plus une science exacte

. Beaucoup de procédés et formulations sont obtenues par essais erreur, encore aujourd'hui sans forcément associer une explication rationnelle.
Par ex en ces jours dans ma boutique certaines unités (on va dire celles qui font la base des peintures à la mode) sont arrétées pas à cause de la crise hémoroïdaire des financiers , mais par non maîtrise des phénomènes tu a plusieurs rangées d'ingénieurs et chercheurs qui se battent avec une explication différente pour décrire le pourquoi de la chose.
Longue vie à la chimie française

Comme tu peux le constater je le prend bien au 4 emme degré
Christophe